Print Powder Development
Producing a reliable, homogenous, and effective wax-based print powder proved to be quite challenging. In order ot be successful, the print powder had to have a fine particle size, had to easily absorb the laser, and had to fuse together into continuous regions with minimal thermal warping.
I produced early print powders by mixing ethanol, dry ice, and paraffin prills (small beads) in a blender. The wax had to be cooled so that impacts from the blender blades would shatter fragments rather than deform them. Ethanol provided both an effective low-temperature medium to conduct heat out of the wax. It also aided the powdering process by keeping the wax localized in the blender, preventing fragments from escaping the blades. The blending process yielded a bubbling slurry that I would leave overnight to allow the alcohol to evaporate and the dry ice to finish sublimating. I then mixed the resulting powder with additional powdered activated carbon to prevent clumping and passed mixture through a screen to ensure homogeneity.
The blender method allowed me to complete many of my early investigations in print powder formulations but it was abandoned to the complexity and length of time necessary for the process.

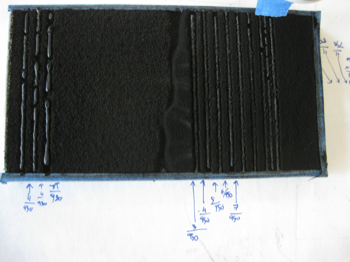
Left: early sintering tests on blender-produced powder. Right: coarser blender-produced print powder compared with finer ball-milled powder.
Next, I investigated a chilled ball-milling approach, which yielded interesting results. I placed dry ice and steel ball bearings into a steel cylinder that I then spun at low speeds in a lathe until the ball bearings reached the temperature of the dry ice. I then introduced paraffin prills and carbon powder along with more dry ice and spun the cylinder again. A small vent hole located in the exposed end of the cylinder allowed pressure and processed powder to escape the vessel. Particles of wax and carbon powder that were small enough to remain suspended in the atmosphere of cylinder as it turned were expelled from the cylinder into a second vessel. With this method, I was able to achieve a very fine and consistent powder size, but separate batches yielded drastically different sintering performances due to inconsistent carbon to wax ratios produced by the process.
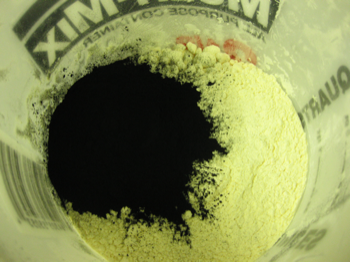
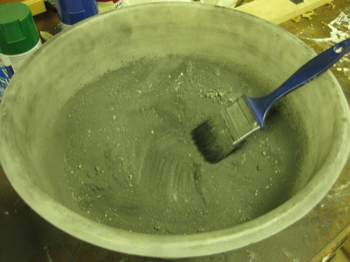
Mixing commercially manufactured candelilla powder with carbon powder and mixing through a sieve.
As it became clear that homebrew powdering methods were not time-efficient, I tested commercially-manufactured wax powders, beginning with the successful ratios of carbon to wax that I had demonstrated in earlier experiments. Though these experiments, I discovered that I needed to adjust the ratio of carbon to wax to compensate for the increased surface area of the finer wax particles. I suspected that too much carbon powder would saturate the print mixture, preventing molten particles of wax from coalescing during sintering. I explored new carbon to wax ratios and settled on a reliable combination of candelilla wax and carbon powder that consistently delivered robust sintering.
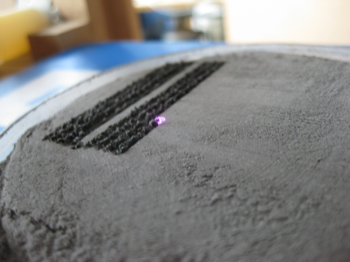
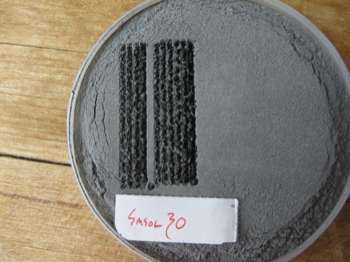
Experimental mixtures of commercial wax and carbon powder. Note the lack of any continuous bead formation.
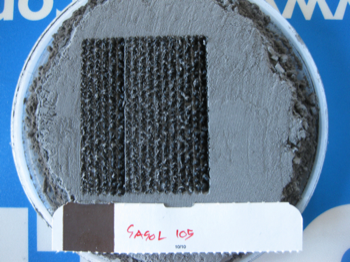
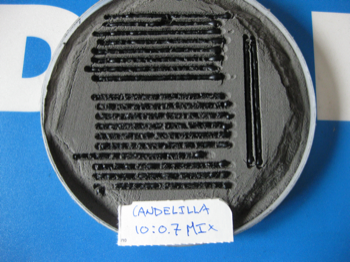
Left: an unsuccessful print mixture. Right: the first successful blend of candelilla wax and carbon powder.
To facilitate my investigation of sintering parameter combinations, I employed a simple scale of "sinter indices" beginning at 0, denoting no sintering action, and ending at 5, denoting perfect sintering.
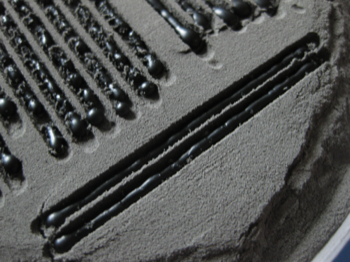
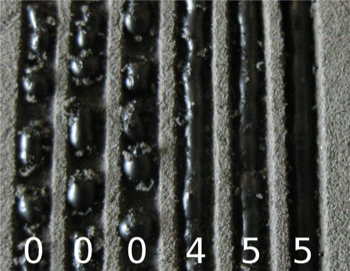
Left: sinter tests of the candelilla mixture. Right: examples of assigned sinter indices.
After discovering a robust set of sintering parameters, I explored the spacing between beads necessary to form sheets of wax. If I could then sinter a new sheet onto a previous sheet, I could achieve the fundamental operation of SLS 3D printing.
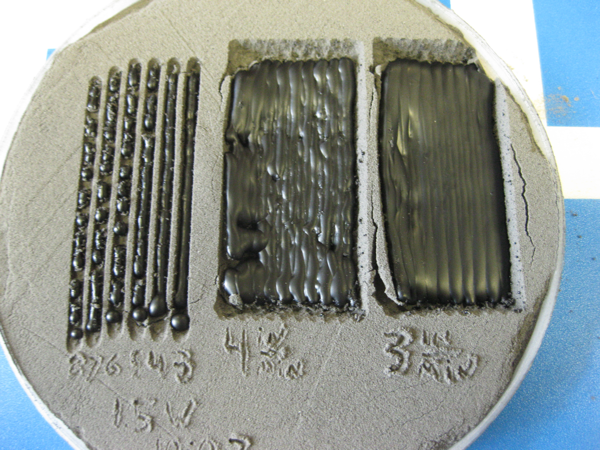
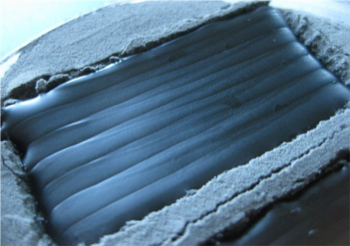